Inexpensive ERP
Sounds like an oxymoron, but there are low-cost ERP systems. More surprising is they do an adequate job. Will you have sophisticated planning options like days supply? No, but you can get a true Materials Requirement Plan run, and it won’t cost you a million dollars.
First, Sixth Floor Consulting Group is not a VAR (Value Added Reseller) for any software products. We have nothing to gain by having any of our partners purchase any particular ERP software package.
Our definition of inexpensive is a company can purchase 10 seats for less than $10,000 in software costs. See below for a better explanation of what the true costs would be for implementing a software package. These packages need to deliver the following minimum functionality to be acceptable:
- Financials – G/L, A/P, A/R, basic costing
- Inventory Control – add, subtract, transfer inventory and physical inventory (cycle counting)
- Manufacturing – production orders, shop floor control, routings
- Sales – customer orders, shipping, invoicing
- Purchasing – purchase orders, RFQ, receiving
Contact Sixth Floor Consulting Group for further information and help with this topic.
Total Cost of Ownership (TCO)
Any company contemplating a software purchase should look at the total cost of owning that software. Besides the cost of the actual software, the following expenses should be budgeted for:
- Hardware and/or Supplementary Software – Does the software require your company purchase a new server or change your current Operating System?
- Data Integration – Your current system data needs to be migrated to the new system. Whether this is a data load from spreadsheets or manually keyed, this cost needs to be factored in.
- Education and Training – The single most important item to ensure a successful software implementation is properly training the system users. Unfortunately, many companies spend more time researching new software than training their employees to use it properly.
Every company’s situation is different on what the above costs will add to an implementation. A good rule of thumb is to add 2 to 4 times the software cost to arrive at the true TCO. This multiplier is highest on the extremes (most expensive and least expensive).
Comparison between Visual Jobshop and MRP+
These are rough approximations of functionality. As each business has different needs a thorough review of all software is required to see if it meets your needs.
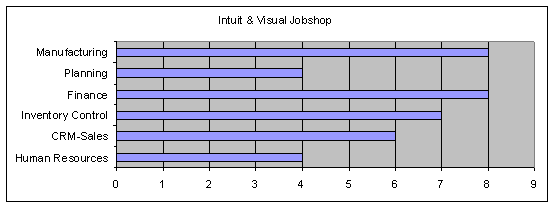
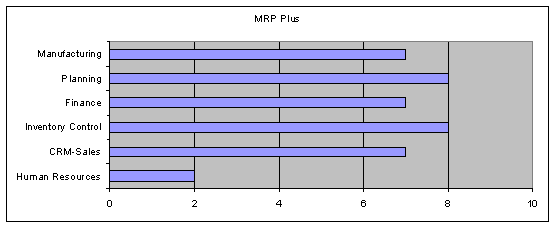
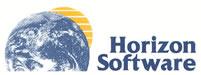
MRP Plus Software
MRP+ software is a complete ERP package with manufacturing, distribution, customer service, and financials included. The software has complete planning functionality including Capacity Planning. The software is written in Microsoft Access, and the source code for forms and reports are provided to companies purchasing MRP+, making customization of these easy and inexpensive. Pricing is $595 per user for 5 – 9 users and $525 per user for 10 – 50 users.
Strengths
- Uses the standard Microsoft GUI interface, and reports can easily be saved as Word Docs or Excel Spreadsheets.
- Has a fully functioning MRP process, and allows the easy conversion of the output into either work orders or purchase orders.
- Allows creation of non-stocked materials (i.e. tools, utilities, etc.).
- Sales orders can have multiple delivery dates.
- <st1:place w:st="on"><st1:placename w:st="on">Work<st1:placetype w:st="on">Center capacity and costs can be based on either machine or labor time.
- Work and Purchase Orders can be planned using multiple different criteria (i.e. planner, buyer, vendor, machine, etc.).
- Has an excellent search function allowing the user to easily find customers or vendors in look up mode.
Weaknesses
- Cost building and roll up is complex without adding enough value.
- Creating the G/L calendar is slow and very manual.
- Could use more tables to limit information that should be standardized (i.e. State is a text field, is Montana MO, MA, or MT?).
- Labor tracking is cumbersome, and needs to be thoroughly thought out before implementing.
Visual Jobshop with Quickbooks Pro
Visual Jobshop is written in Microsoft Access, and has a built in interface to either QuickBooks or Peachtree accounting software. Cost will be based on which version of Quickbooks (or Peachtree) is used, along with number of seats for each package. An estimate is $1,000 for 3 Quickbook pro seats + $1,200 a seat for Visual Jobshop.
Strengths
- Has multiple Units Of Measure and supports pre-defining these (i.e. inches to feet). Also, allows user to set number of decimal places for each UOM.
- Allows multiple pricing options and price points.
- Strong quoting system which allows converting quote to a new item and/or new customer. Quote can also be converted to a work order if sales order comes out of quote process.
- Has a good integrated BOM/Routing structure with visual representation of processes and materials needed to build an item.
- Detailed specs and pictures can be stored on the item master.
- System supports outside services as part of the production process. Will incorporate those costs in the roll up.
- Machines can be grouped for easier scheduling (i.e. all Bridgeports together so an item can be scheduled on any open machine).
- Uses the standard Microsoft GUI interface, and reports can easily be saved as Word Docs or Excel Spreadsheets.
Weaknesses
- Planning is not a full MRP and is triggered by reorder points. Does allow min/max and multiples ordering.
- Because financials are a separate system, running of interface becomes critical to updating books. Always have the possibility of duplicate information in the financials.
- Visual Jobshop interfaces to financials; there is no interface back to manufacturing.
- It is a three step process to key production into the system (i.e. labor, materials, final product receipt).